PRODUCTS
Contact us
86 17344894490Mobile:86 17344894490
Email:info@signialuminium.com
Skype:signialuminio
Sales Office:A126 Building 4, No.89 Science Avenue,National HI-Tech Industry Development Zone,Zhengzhou,Henan,China
Factory Address:Industrial District, Xin'an, Luoyang city, Henan Province,China
polished aluminium sheet plate
Current :Home/polished aluminium sheet plate /
polished aluminium sheet plate
Time :2022/03/23 Click :
0 Preface
The surface brightness of polished aluminum sheet products is close to or equal to that of the mirror, with high surface gloss and fine lines. It is mostly used in the field of reflective lighting, indoor and outdoor architectural decoration, automobile interior and exterior decoration, high-grade switch panel and various high-grade signs and nameplates (external labels of foreign wine), etc. Because the product belongs to aluminum alloy plate and strip with ultra-high surface quality requirements, it is very difficult to research and develop the product. Some domestic aluminum calendering enterprises also develop the product, but the effect is not satisfactory, mainly manifested in the problems of rough surface texture, low gloss, many surface quality defects and so on. In 2012, based on the existing tooling conditions, our company used 1400mm cold rolling mill to study the process of 1070 aluminum alloy polished aluminum sheet. Through the process research, the difficult problems such as poor surface brightness, rough texture and many surface quality defects have been gradually solved, so that our company can stably produce polished aluminum sheet products with high surface reflectivity, and the longitudinal gloss can stably reach more than 780gs, up to 820gs, meeting the needs of the domestic market. Some products can replace the imported polished aluminum sheet, It breaks the long-term dependence on imports of domestic high-grade polished aluminum sheet products, which is of great significance.
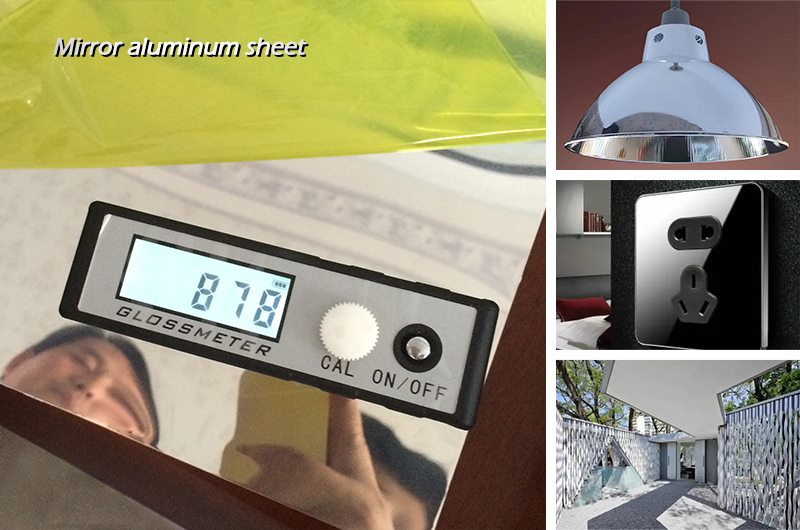
The following focuses on the research and development of the production process of the polished aluminum sheet, as well as the influence of process lubrication, pass processing rate and other parameters on the quality of the polished aluminum sheet in the rolling process.
1 technical proposal
At present, 1070 aluminum alloy is mainly used for rolling polished aluminum sheet, supplemented by 3-Series and 8-series aluminum alloys. 1070 aluminum alloy is used as the test material in this technical scheme. 1450mm cold roughing mill is used to produce open passes and intermediate passes, and 1400mm cold finishing mill is used to produce product passes. On the premise of using the existing equipment for producing ordinary aluminum strip, the purpose of producing high brightness and high quality polished aluminum sheet is achieved by grinding the work roll of 1450mm cold roughing mill and 1400mm cold finishing mill and controlling and adjusting the rolling process of 1400mm cold finishing mill.
The production process of 1070 polished aluminum sheet cold rolling is as follows: the thickness of hot rolling billet is 6.0 ~ 6.5mm → 1450 rolling mill is rolled to (1.6 ± 0.03) mm → finishing cleaning → intermediate annealing → 1450 rolling mill is rolled to (0.63 ± 0.01) mm → finishing cleaning and trimming → 1400 rolling mill is rolled to the thickness of finished products.
(1) Open rolling: 1450 rolling mill rolls three passes from the billet thickness of 6.0 ~ 6.5mm to (1.6 ± 0.03) mm. Reference track arrangement: 6.3, 4.0, 2.8, 1.6.
(2) Secondary rolling: 1450 rolling mill is used to roll from (1.6 ± 0.03) mm to (0.63 ± 0.01) mm. Reference pass arrangement: 1.6, 0.9, 0.63.
(3) Finished product rolling: 1400 rolling mill is polished and rolled from 0.63mm to the thickness of finished product. About 15% rolling reduction according to the reference rolling amount.
2 process technology research
2.1 work roll grinding
2.1.1 grinding of work roll of 1450mm cold rolling mill The work roll grinding of 1450mm cold roughing mill is mainly divided into three stages: rough grinding, medium grinding and fine grinding. All three stages of grinding use 100# ceramic grinding wheel. The rough grinding stage mainly grinds the hardened layer of the old roll surface and obvious defects on the roll surface; The intermediate grinding stage is to eliminate the knife marks left by rough grinding and prepare for fine grinding roll shape; The precise roll shape is finally obtained in the fine grinding stage. The roll shape of the work roll is -0.02mm up and down, and the roughness Ra = 0.20 ~ 0.25 μ m. Ensure that the roll surface quality is free of obvious helix, "weaving pattern", vibration pattern and other grinding roll defects. The grinding process of work roll of 1450mm rolling mill is shown in Table 1.
2.1.2 work roll grinding of 1400mm cold finishing mill
The traditional roll surface processing technology is difficult to meet the requirements of polished aluminum sheet. It is necessary to study a new roll surface processing technology so that the roll surface roughness can reach 0.008 ~ 0.010 μ m。 At present, the process technologies used to improve roll roughness mainly include: roll grinder fine grinding and polishing process, sandpaper tape polishing process and electrochemical precision mechanical vibration polishing process. According to the actual situation, we use roll grinder to finish grinding and polishing process.
The grinding of work roll of 1400mm cold finishing mill is completed by special grinding process on the company's 1# grinder, and the roll shape is up and down + 0.055mm. Firstly, the same grinding process as the work roll grinding of 1450 rolling mill is used; Secondly, 320 # and 500 # resin grinding wheels are used for deep fine grinding; Finally, 1000# graphite grinding wheel is used for polishing and grinding, and finally the mirror roller with "double zero" roughness is obtained. The depth grinding process and polishing process of mirror roll of 1400mm rolling mill are shown in Table 2.
2.2 cold rolling process
The cold rolling of aluminum strip is an independent process, and its processing degree plays an important role in the surface brightness of aluminum strip. The opening pass and intermediate pass of 1450mm rolling mill shall be rolled according to the standard for the production of ordinary strip, laying a foundation for the polishing rolling of 1400mm cold rolling mill. The difficulty and key points of polished aluminum sheet rolling mainly lie in the rolling of 1400mm cold rolling mill.
In order to obtain the polished aluminum sheet with bright surface and fine grain, in addition to the work roll with low roughness, we should also study the influence of process lubrication, pass reduction, rolling speed and rolling pass in the rolling process.
2.2.1 process lubrication
The effect of process lubrication on the gloss of rolling surface is realized by the thickness of oil film formed in the deformation zone. The thickness of oil film depends on the polarity and chain length of additives, which leads to the difference of friction effect, and then affects the surface brightness of aluminum plate after rolling. When the additive ratio of rolling oil is low, it lacks the oil molecules necessary to form the basic oil film, can not form fluid lubrication, the roughness increases and the gloss decreases; When the proportion of additives is high, the thickness of oil film is too thick, and the "shielding effect" of oil film in the deformation area makes the surface roughness of roll unable to be transmitted to the surface of aluminum plate, which also fails to meet the required gloss.
The roughness of work roll required by 1400 rolling mill is very low, the friction coefficient is small, and the requirements for 1400mm rolling lubrication conditions are relatively harsh. Therefore, it is particularly critical to explore a reasonable proportion of additives. Our company adopts the existing Qingjiang Petrochemical 85# base oil and medium aluminum lubricating 10# and 12# additives to form the lubricating medium in the ratio of 1:3. After analysis, research and field tests, rolling tests were carried out for the proportion of additives of 3%, 5%, 8% and 12% respectively. The results show that when the additive ratio of 1400mm cold rolling mill is kept at 8%, 10# and 12# ratio is kept at 1 ∶ 3, the surface texture of aluminum strip is fine and the gloss is high. When the additive ratio is 12% and 5%, the surface of the rolled plate is rough or the color difference is large.
2.2.2 pass reduction
Mirror rolling belongs to polishing rolling. When the reduction is too large, the thickness of oil film in the deformation area is reduced, and the surface roughness of rolled plate is also reduced; When the rolling pressure increases to a certain value, after the oil film thickness reaches the minimum critical condition of fluid lubrication, it will not be thinned, and the surface roughness tends to be stable; When the rolling force continues to increase and is greater than the molecular oil film bearing limit, the oil film breaks and the roll directly contacts the surface of the rolled plate to form dry friction, resulting in extremely uneven surface roughness of the aluminum plate, i.e. pine tree branch pattern defects [3]. On the contrary, when the reduction is too small, the oil film in the deformation area becomes thicker, making the surface of the rolled plate thicker. The relationship between the reduction rate and the surface brightness of aluminum plate after cold rolling is shown in Figure 1.
Referring to the 40 ℃ kinematic viscosity of kerosene in Figure 1, combined with the equipment properties of the company's 1400mm rolling mill, the kinematic viscosity of oil and the alloy state of the test material, the processing rates of 5%, 10%, 15%, 20% and 25% are set for the material with a thickness of 0.3mm. The test results are shown in Table 3.
It can be seen from the results in Table 3 that when the thickness of rolled finished aluminum strip is 0.3mm, the surface gloss of aluminum plate under 10% reduction is the best, and there is little difference between it and 5% reduction. 10% reduction is recommended for industrial production.
2.2.3 rolling speed
The influence of rolling speed on the surface quality of rolled plate is mainly reflected by the lubrication condition. With the increase of rolling speed, more rolling oil enters into the roll gap, the oil film in the deformation zone becomes thicker, and it is easy to form over lubrication. Due to the extremely low roughness of the roll used for rolling polished aluminum sheet, when rolling 0.3mm thick material and the rolling speed reaches 150m / min, there will be serious slip, resulting in obvious chattering on the surface of the rolled plate and poor shape, which can not be controlled. Normal rolling can be carried out when the rolling speed is reduced to 120m / min, 100M / min, 80m / min, 60m / min, 30m / min and 10m / min respectively. According to the actual detection of surface gloss, the surface gloss of rolled plate is the best when the speed is 30m / min, as shown in Table 4.
It can be seen from table 4 that when rolling 0.3mm thick aluminum strip, the surface gloss of the rolled plate is the best at the rolling speed of 30m / min, followed by the speeds of 10m / min and 60m / min. From the perspective of industrial continuous production, 60m / min rolling speed can be adopted.
2.2.4 rolling passes
When rolling ordinary products, the roll surface roughness will decrease with the increase of rolling passes. When it is reduced to a certain extent, the roughness will not decrease. In the rolling of polished aluminum sheet, the roughness of its own roll has been very low. After field verification, the increase of rolling passes has little effect on the roughness of the roll. On the contrary, the rolling passes of the test coil increase, and the surface gloss of the aluminum plate increases continuously. When the surface gloss of aluminum plate reaches a certain value, increasing rolling passes will not improve the surface gloss of aluminum plate. Therefore, through the verification of multiple rounds of tests, according to the product thickness, rolling 3 ~ 5 passes can make the aluminum plate achieve the ideal gloss, and increasing the passes has little significance to improve the gloss.
3 conclusion
Through the practice of multi batch rolling production on the production site, the process is stable and mature, can realize batch production, and creates good product competitiveness and economic benefits for the enterprise.
The surface brightness of polished aluminum sheet products is close to or equal to that of the mirror, with high surface gloss and fine lines. It is mostly used in the field of reflective lighting, indoor and outdoor architectural decoration, automobile interior and exterior decoration, high-grade switch panel and various high-grade signs and nameplates (external labels of foreign wine), etc. Because the product belongs to aluminum alloy plate and strip with ultra-high surface quality requirements, it is very difficult to research and develop the product. Some domestic aluminum calendering enterprises also develop the product, but the effect is not satisfactory, mainly manifested in the problems of rough surface texture, low gloss, many surface quality defects and so on. In 2012, based on the existing tooling conditions, our company used 1400mm cold rolling mill to study the process of 1070 aluminum alloy polished aluminum sheet. Through the process research, the difficult problems such as poor surface brightness, rough texture and many surface quality defects have been gradually solved, so that our company can stably produce polished aluminum sheet products with high surface reflectivity, and the longitudinal gloss can stably reach more than 780gs, up to 820gs, meeting the needs of the domestic market. Some products can replace the imported polished aluminum sheet, It breaks the long-term dependence on imports of domestic high-grade polished aluminum sheet products, which is of great significance.
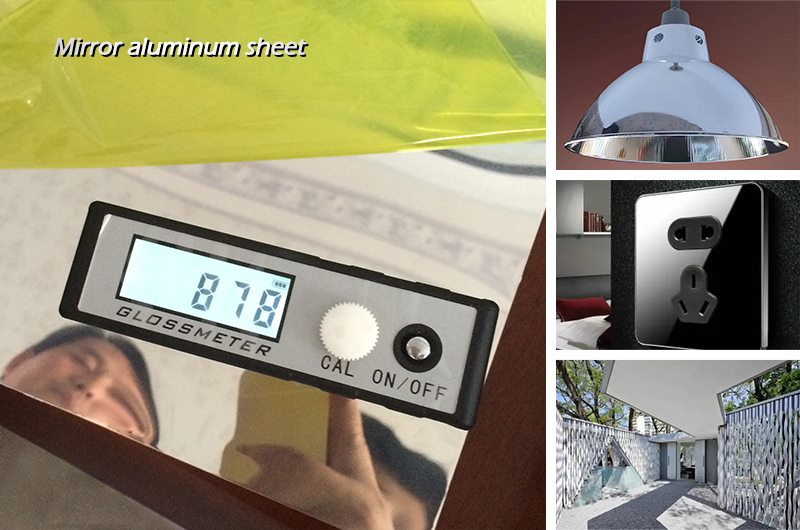
The following focuses on the research and development of the production process of the polished aluminum sheet, as well as the influence of process lubrication, pass processing rate and other parameters on the quality of the polished aluminum sheet in the rolling process.
1 technical proposal
At present, 1070 aluminum alloy is mainly used for rolling polished aluminum sheet, supplemented by 3-Series and 8-series aluminum alloys. 1070 aluminum alloy is used as the test material in this technical scheme. 1450mm cold roughing mill is used to produce open passes and intermediate passes, and 1400mm cold finishing mill is used to produce product passes. On the premise of using the existing equipment for producing ordinary aluminum strip, the purpose of producing high brightness and high quality polished aluminum sheet is achieved by grinding the work roll of 1450mm cold roughing mill and 1400mm cold finishing mill and controlling and adjusting the rolling process of 1400mm cold finishing mill.
The production process of 1070 polished aluminum sheet cold rolling is as follows: the thickness of hot rolling billet is 6.0 ~ 6.5mm → 1450 rolling mill is rolled to (1.6 ± 0.03) mm → finishing cleaning → intermediate annealing → 1450 rolling mill is rolled to (0.63 ± 0.01) mm → finishing cleaning and trimming → 1400 rolling mill is rolled to the thickness of finished products.
(1) Open rolling: 1450 rolling mill rolls three passes from the billet thickness of 6.0 ~ 6.5mm to (1.6 ± 0.03) mm. Reference track arrangement: 6.3, 4.0, 2.8, 1.6.
(2) Secondary rolling: 1450 rolling mill is used to roll from (1.6 ± 0.03) mm to (0.63 ± 0.01) mm. Reference pass arrangement: 1.6, 0.9, 0.63.
(3) Finished product rolling: 1400 rolling mill is polished and rolled from 0.63mm to the thickness of finished product. About 15% rolling reduction according to the reference rolling amount.
2 process technology research
2.1 work roll grinding
2.1.1 grinding of work roll of 1450mm cold rolling mill The work roll grinding of 1450mm cold roughing mill is mainly divided into three stages: rough grinding, medium grinding and fine grinding. All three stages of grinding use 100# ceramic grinding wheel. The rough grinding stage mainly grinds the hardened layer of the old roll surface and obvious defects on the roll surface; The intermediate grinding stage is to eliminate the knife marks left by rough grinding and prepare for fine grinding roll shape; The precise roll shape is finally obtained in the fine grinding stage. The roll shape of the work roll is -0.02mm up and down, and the roughness Ra = 0.20 ~ 0.25 μ m. Ensure that the roll surface quality is free of obvious helix, "weaving pattern", vibration pattern and other grinding roll defects. The grinding process of work roll of 1450mm rolling mill is shown in Table 1.
2.1.2 work roll grinding of 1400mm cold finishing mill
The traditional roll surface processing technology is difficult to meet the requirements of polished aluminum sheet. It is necessary to study a new roll surface processing technology so that the roll surface roughness can reach 0.008 ~ 0.010 μ m。 At present, the process technologies used to improve roll roughness mainly include: roll grinder fine grinding and polishing process, sandpaper tape polishing process and electrochemical precision mechanical vibration polishing process. According to the actual situation, we use roll grinder to finish grinding and polishing process.
The grinding of work roll of 1400mm cold finishing mill is completed by special grinding process on the company's 1# grinder, and the roll shape is up and down + 0.055mm. Firstly, the same grinding process as the work roll grinding of 1450 rolling mill is used; Secondly, 320 # and 500 # resin grinding wheels are used for deep fine grinding; Finally, 1000# graphite grinding wheel is used for polishing and grinding, and finally the mirror roller with "double zero" roughness is obtained. The depth grinding process and polishing process of mirror roll of 1400mm rolling mill are shown in Table 2.
2.2 cold rolling process
The cold rolling of aluminum strip is an independent process, and its processing degree plays an important role in the surface brightness of aluminum strip. The opening pass and intermediate pass of 1450mm rolling mill shall be rolled according to the standard for the production of ordinary strip, laying a foundation for the polishing rolling of 1400mm cold rolling mill. The difficulty and key points of polished aluminum sheet rolling mainly lie in the rolling of 1400mm cold rolling mill.
In order to obtain the polished aluminum sheet with bright surface and fine grain, in addition to the work roll with low roughness, we should also study the influence of process lubrication, pass reduction, rolling speed and rolling pass in the rolling process.
2.2.1 process lubrication
The effect of process lubrication on the gloss of rolling surface is realized by the thickness of oil film formed in the deformation zone. The thickness of oil film depends on the polarity and chain length of additives, which leads to the difference of friction effect, and then affects the surface brightness of aluminum plate after rolling. When the additive ratio of rolling oil is low, it lacks the oil molecules necessary to form the basic oil film, can not form fluid lubrication, the roughness increases and the gloss decreases; When the proportion of additives is high, the thickness of oil film is too thick, and the "shielding effect" of oil film in the deformation area makes the surface roughness of roll unable to be transmitted to the surface of aluminum plate, which also fails to meet the required gloss.
The roughness of work roll required by 1400 rolling mill is very low, the friction coefficient is small, and the requirements for 1400mm rolling lubrication conditions are relatively harsh. Therefore, it is particularly critical to explore a reasonable proportion of additives. Our company adopts the existing Qingjiang Petrochemical 85# base oil and medium aluminum lubricating 10# and 12# additives to form the lubricating medium in the ratio of 1:3. After analysis, research and field tests, rolling tests were carried out for the proportion of additives of 3%, 5%, 8% and 12% respectively. The results show that when the additive ratio of 1400mm cold rolling mill is kept at 8%, 10# and 12# ratio is kept at 1 ∶ 3, the surface texture of aluminum strip is fine and the gloss is high. When the additive ratio is 12% and 5%, the surface of the rolled plate is rough or the color difference is large.
2.2.2 pass reduction
Mirror rolling belongs to polishing rolling. When the reduction is too large, the thickness of oil film in the deformation area is reduced, and the surface roughness of rolled plate is also reduced; When the rolling pressure increases to a certain value, after the oil film thickness reaches the minimum critical condition of fluid lubrication, it will not be thinned, and the surface roughness tends to be stable; When the rolling force continues to increase and is greater than the molecular oil film bearing limit, the oil film breaks and the roll directly contacts the surface of the rolled plate to form dry friction, resulting in extremely uneven surface roughness of the aluminum plate, i.e. pine tree branch pattern defects [3]. On the contrary, when the reduction is too small, the oil film in the deformation area becomes thicker, making the surface of the rolled plate thicker. The relationship between the reduction rate and the surface brightness of aluminum plate after cold rolling is shown in Figure 1.
Referring to the 40 ℃ kinematic viscosity of kerosene in Figure 1, combined with the equipment properties of the company's 1400mm rolling mill, the kinematic viscosity of oil and the alloy state of the test material, the processing rates of 5%, 10%, 15%, 20% and 25% are set for the material with a thickness of 0.3mm. The test results are shown in Table 3.
It can be seen from the results in Table 3 that when the thickness of rolled finished aluminum strip is 0.3mm, the surface gloss of aluminum plate under 10% reduction is the best, and there is little difference between it and 5% reduction. 10% reduction is recommended for industrial production.
2.2.3 rolling speed
The influence of rolling speed on the surface quality of rolled plate is mainly reflected by the lubrication condition. With the increase of rolling speed, more rolling oil enters into the roll gap, the oil film in the deformation zone becomes thicker, and it is easy to form over lubrication. Due to the extremely low roughness of the roll used for rolling polished aluminum sheet, when rolling 0.3mm thick material and the rolling speed reaches 150m / min, there will be serious slip, resulting in obvious chattering on the surface of the rolled plate and poor shape, which can not be controlled. Normal rolling can be carried out when the rolling speed is reduced to 120m / min, 100M / min, 80m / min, 60m / min, 30m / min and 10m / min respectively. According to the actual detection of surface gloss, the surface gloss of rolled plate is the best when the speed is 30m / min, as shown in Table 4.
It can be seen from table 4 that when rolling 0.3mm thick aluminum strip, the surface gloss of the rolled plate is the best at the rolling speed of 30m / min, followed by the speeds of 10m / min and 60m / min. From the perspective of industrial continuous production, 60m / min rolling speed can be adopted.
2.2.4 rolling passes
When rolling ordinary products, the roll surface roughness will decrease with the increase of rolling passes. When it is reduced to a certain extent, the roughness will not decrease. In the rolling of polished aluminum sheet, the roughness of its own roll has been very low. After field verification, the increase of rolling passes has little effect on the roughness of the roll. On the contrary, the rolling passes of the test coil increase, and the surface gloss of the aluminum plate increases continuously. When the surface gloss of aluminum plate reaches a certain value, increasing rolling passes will not improve the surface gloss of aluminum plate. Therefore, through the verification of multiple rounds of tests, according to the product thickness, rolling 3 ~ 5 passes can make the aluminum plate achieve the ideal gloss, and increasing the passes has little significance to improve the gloss.
3 conclusion
Through the practice of multi batch rolling production on the production site, the process is stable and mature, can realize batch production, and creates good product competitiveness and economic benefits for the enterprise.